pressure limiter
HCB-DPL (Digital Preasure Limiter)
In normal operation, the limit pressure is set analogously. Below the limit pressure, the pressure limiter works as a normal proportional amplifier for hydraulic axles.
Inputs and outputs:
- Digital inputs, depending on the application, can be parameterized as release for various functions, ramp selection, parameter set changeover, volume fixed values, pressure fixed values, direction reversal, etc.
- Frequency inputs for recording the actual diesel speed per axle
- Analog inputs for the analog volume and pressure set values as well as the actual pressure values per axle
- Proportional outputs with current feedback measurement for 2 pumps forward/reverse
- Status outputs “Limitation active”
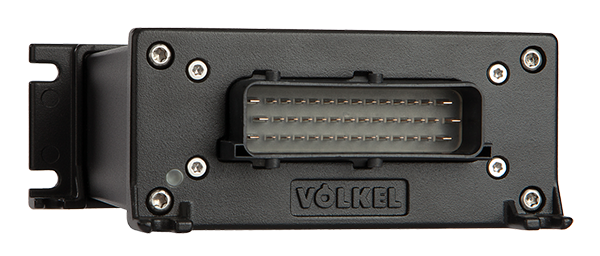
Detailed information on the DPL
In normal operation, the limit pressure is set analogously. Below the limit pressure, the pressure limiter works as a normal proportional amplifier for hydraulic axles.
Accordingly, the specified set values from setpoint generators, higher-level controllers or sensors are read in and mapped to proportional currents to control the solenoids of pumps. If the pressure limiter is activated, the volume and thus the pressure is reduced in accordance with the set and calculated pressure set value if the actual pressure value exceeds the pressure set value.
The DPL can also be operated as a pressure regulator. In this operating mode, a limit value is set for the volume and the pressure set value is varied analogously. Below the limit volume, the DPL then works as a pressure regulator.
The standard hardware platform for the pressure limiter is the HCB controller. Two pumps can be controlled bi-directionally. If the DPL is to be integrated into a machine control system, it can easily be ported to another Völkel hardware platform.
A special feature of the operating mode as a pressure regulator is that only the high pressure A is measured. A control strategy has been implemented with which it is possible to control the pump by zero in the opposite direction in the event of back pressure generated by the hydraulic motor. The regulator is therefore particularly suitable for winches in shipping where the rope must always be kept under tension even in DPL swell or currents (mooring system). An additional frequency input for each axle makes it possible to detect and compensate for fluctuations in the speed of the drive unit in order to keep the desired volume flow constant. If the pump needs to be able to run very precisely through zero, the volume flow needs to be controlled very precisely or it needs to follow even small setpoint jumps very precisely and quickly, the pump swivel angle can be recorded and controlled.
In normal operation, the DPL is used in drilling rigs, for example, where the pressure on the drill bit needs to be limited. It is used as a pressure regulator for anchor winches, mooring control, etc.
Inputs and outputs
- Digital inputs, depending on the application, can be parameterized as release for various functions, ramp selection, parameter set changeover, volume fixed values, pressure fixed values, direction reversal, etc.
- Frequency inputs for recording the actual diesel speed per axle
- Analog inputs for the analog volume and pressure set values as well as the actual pressure values per axle
- Proportional outputs with current feedback measurement for 2 pumps forward/reverse
- Status outputs “Limitation active”

Control unit: HCB / Application: DPL (Digital Preasure Limiter)
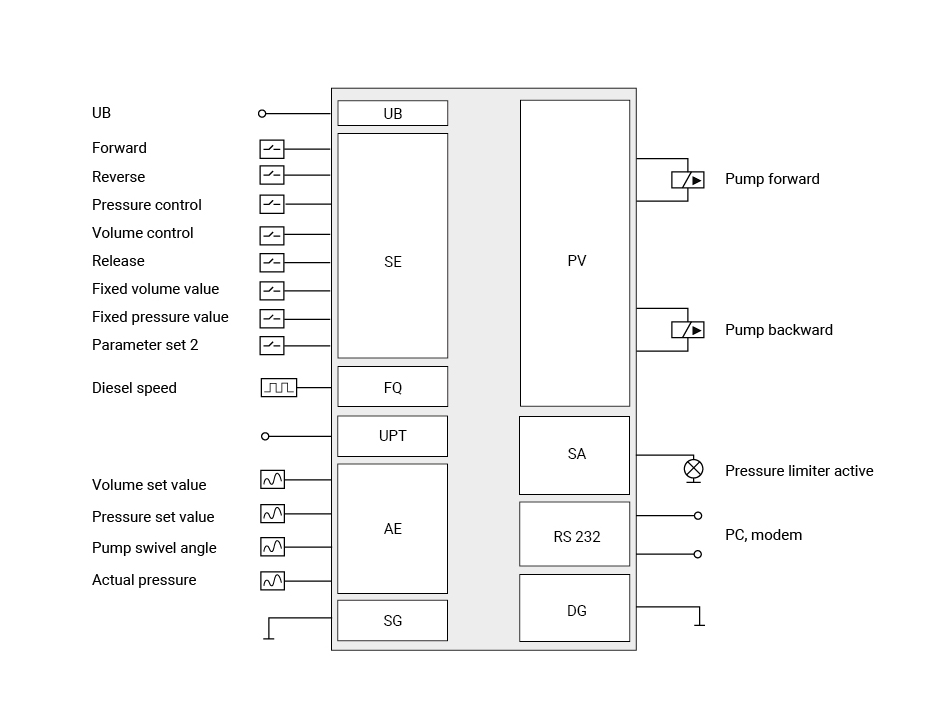
What can we do for you?
Get in touch

R. Umar B.Sc.
Phone +49 2534 9731-504
Mobile +49 170 3705711
umar@voelkel.de
Völkel Mikroelektronik GmbH
Otto-Hahn-Straße 30
48161 Münster